Laser monitoring system adds extra dimension to 3D printing
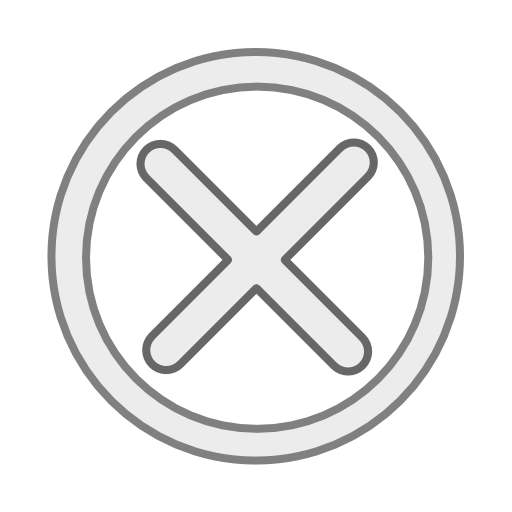
In fields such as aerospace and medical equipment, the production of complex components often presents significant challenges, but the advent of 3D printing has provided an effective solution.
In the scientific community, the technology of manufacturing solid parts by gradually accumulating materials is known as additive manufacturing, more commonly referred to as 3D printing. Compared with traditional methods of making parts, 3D printing offers greater freedom, stronger capability for producing complex shapes, and greater efficiency.
Additive manufacturing technology is being applied in various fields, including aerospace, healthcare, the automotive industry, consumer goods, construction and education.
Nearly 37 million consumer product parts were manufactured using 3D printing in 2023, marking a 23 percent increase from 2022, according to a report by market researcher VoxelMatters.
In 2023 alone, polymer 3D printing produced 16.8 million parts, while metal 3D printing produced 364,000 parts. For instance, 15 percent of the parts in the VK-650V and VK-1600V helicopter engines from Russia's Klimov company, including casing parts and injectors, were produced by 3D printers.
However, Professor Chen Xuefeng from the iHarbour Academy of Frontier Equipment at Xi'an Jiaotong University issued a note of warning about 3D printing. "During mass production, additive manufacturing technology faces issues such as quality instability and difficulty in real-time defect detection, which hinder its large-scale application," he said.
Zhang Xingwu, a professor on mechanical engineering at the university, said consistent manufacturing quality is a critical challenge in the mass application of additive manufacturing.
"Currently, most processes involve 'blind' operations, where real-time processing quality is unknown and can only be assessed post-manufacture via offline methods like CT scans. If a part fails to meet standards, it must be scrapped, causing significant financial loss and wasting months," he said.
Researcher Zhao Zhibin cited the example of a complex engine component that might be worth several million yuan. "If defects like gas pockets are discovered after a single 3D printing, the entire component is invalidated, leading to considerable waste," Zhao said.
For mass production using additive manufacturing, a universal quality system needs to be established nationwide, and even globally, Chen said.
Supported by key national R&D projects, Chen's team has developed a set of additive manufacturing monitoring systems over the past few years that use lasers.
According to Zhang, these technologies involve rapid measurement, accurate judgment, and steady control. Due to the highly variable states in metal additive manufacturing a swift process is required to obtain real-time information.
"In mass production, there are a few critical steps that must be periodically monitored," said Chen.
The laser monitoring system enables real-time monitoring during the manufacturing process. This means immediate intervention can be carried out when an error is detected, which can minimize cost. This AI-enhanced technology improves identification precision and reliability by up to 95 percent.
Image recognition driven by artificial intelligence stabilizes algorithms, and allows the technology to quickly generalize patterns from the data.
This system is gradually being implemented, primarily in the aerospace industry, and has been exported to various countries including Austria. "Now, companies purchasing additive manufacturing equipment often acquire the corresponding number of laser monitoring systems," Chen said.
Zhang said the monitoring system is pivotal for enhancing quality consistency. A number of institutions, including the United States' National Institute of Standards and Technology, have consistently emphasizes its importance in official technical documentation, he said.
- Laser monitoring system adds extra dimension to 3D printing
- Consumption push promises summer tourism boom
- Snake-like, miniature robots redefine limits of engineering
- 2,000-year-old steel acupuncture needles unearthed in Jiangxi
- New carbon neutrality initiative launched in Beijing
- Three killed in downtown Guangzhou traffic accident